Container transport companies are having a hard time. They continue to see rising prices of import containers.
Why is this happening?
There are various reasons. Empty container parks (ECP) have reduced the number of vehicles they will accommodate. Huge volumes of containers and redirections are also factors. They directly lead to increases in the costs of handling empty containers.
In Sydney, transport firms are close to giving up. The situation has worsened in recent months and is becoming too difficult to handle. The current global economic situation and the pandemic have also added to their woes. Unless they come up with solutions fast, they will go out of business.
When transporting empty containers, transport firms shoulder about $90-$200 per container. The prices might be higher depending on the extra processing and probable delays.
Let us examine a few important reasons that contribute to Sydney’s rising empty container expenses.
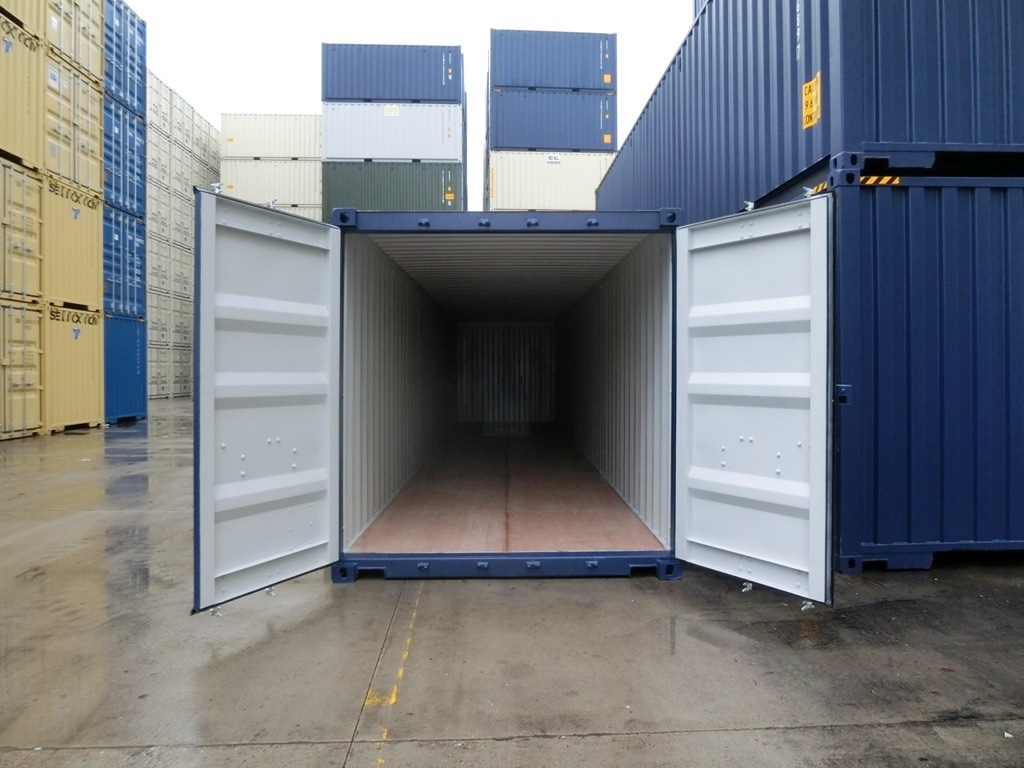
Costs in container parks and transport yards
Prices for available truck arrival slots are higher at key ECPs in Sydney. This is also true for gate capacity. When the ECP’s working hours are irregular, especially on weekends, they also increase their fees even more.
As a result, the bulk of empty containers remain in transport yards. This results in extra expenses. There is always an added cost for more yard planning and management.
One must also prepare for container storage and staging (lift-on and lift-off). You could also incur extra charges due to increased truck travel distance. The same is true for one-way truck travel with limited chances for backloading.
Most transport providers are unable to arrange enough truck arrival slots on time. De-hire delays in ECPs may also occur. Late returns also increase costs due to container detention fees from shipping lines.
Empty container parks and shipping lines should give a 24-hour redirection notice. They should also set a precise end date for empty container redirection. Also, shipping lines should send electronic data to their ECP providers. This way, allocators will no longer have to maintain and track redirection notices.
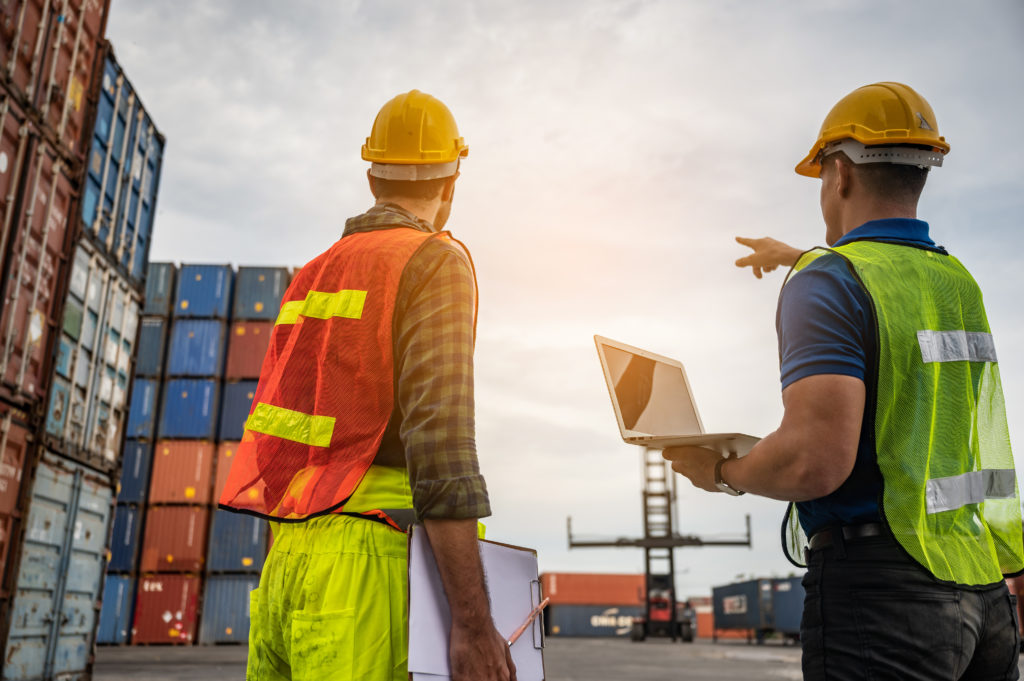
Redirection of containers
There are a huge number of empty container redirections without prior warning. This is one of the primary causes of increasing empty container management expenses.
The redirections are ordered at the discretion of shipping lines, such as Port Botany. With about 30 redirections every day, Port Botany has earned the title of Australia’s “redirection capital.” This is more than twice those in Melbourne. This heavy volume of redirections is why empty container prices continue to rise.
When empty containers are abruptly rerouted, it requires last-minute adjustments. As a result, transport companies’ plans become more complicated.
This happens because shipping lines want the empty containers transported to another ECP for their future use. It means they will no longer bear the expense of relocating empty containers at a later date. They will be able to fulfil rail export needs as a result of this.
These actions give containment logistics companies a hard time. Because of a lack of warning, they need to give extra handling and transportation charges.
As a result, vehicles that already have an ECP arrival notification are turned down. This leads to wasted truck mileage, needless truck trips, de-hire time delays, and a slew of other issues.
Lack of advance notice of a diversion burdens container transport operators.
To fully solve these concerns and decrease empty container expenses, there is a solution. Legitimate truck bookings at ECPs should be honoured. Redirection should also be eliminated. They should put in a place a system that will reward those who follow the rules.
Claims and timeframes issues
There are real difficulties in being efficient at managing empty containers. Shipping lines also do not offer any incentives to lengthen container detention periods.
Because delays and inefficiencies are normal during this pandemic, time constraints will likely be surpassed. But, operators need advance notice for those scheduled for empty de-hire. Many transport firms are not amenable to unreasonable container detention claims. They deem it unfair that they will pay more even when de-hire delays are beyond their control.
Customers and transportation operators can work together to solve this problem.
It is not always the transportation company’s obligation to reduce container detention fees. Also, it should not be the company’s responsibility to pay container detention fees for unforeseen de-hire delays. Besides, they should not shoulder costs due to unrealistic claims and enforced deadlines.
What actions can customers, importers, and forwarders take?
They can request a time extension from the shipping line for the empty container’s return. Asking that they de-hire in an empty container park with more flexible arrangements is a viable alternative. Parks with extended opening hours will also be helpful.
In Sydney, several empty container parks are open for longer hours of operation. More facilities will allow importers, forwarders, and their transportation providers to adjust.
Increased import container costs are straining container shipping companies. Sudden container redirections influence handling costs. Staging of empty containers through yards and unrealistic container detention durations spike prices. When these are resolved, prices will begin to fall at a more reasonable rate.
All stakeholders must make a compromise. They need to arrive at a decision that will be beneficial to everyone. If no one wants to yield, we will see a further decline in the industry.